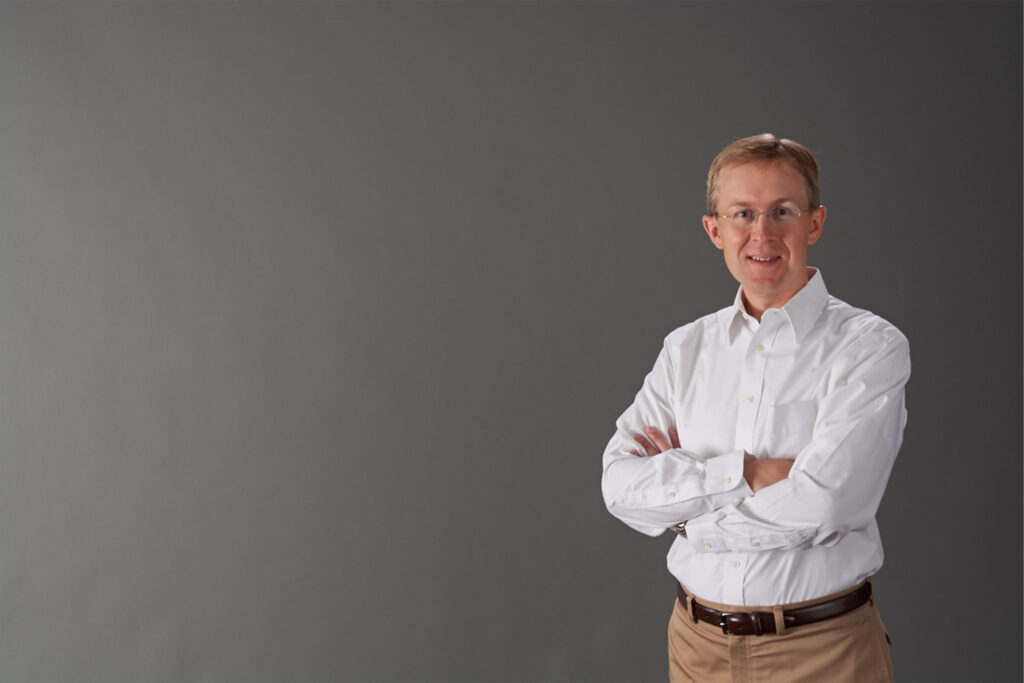
Chaotic storage?
Tell me about it, you say. You’re drowning in it—from the bedroom closet to the kitchen cabinets, and you don’t even want to think about the garage.
But chaotic storage is actually a term for how some of the world’s biggest retail corporations, like Amazon and Walmart, organize inventory on their warehouse floors. While the word “chaotic” might sound negative, it simply means an item is slotted into a warehouse bin wherever there is an available space. Rather than grouping identical inventory items together—all the copies of Fire and Fury together, for example—this type of system maximizes capacity by storing dissimilar products in a single bin. Warehouse workers, called pick-workers, perform a search to find the correct bin and “pick” the item up to ready it for the next stage of sending to the consumer.
Companies like L.L.Bean have shipped one-off orders for years—a headlamp, a camp stove, a fisherman’s sweater—but e-commerce has become a larger part of our economy each year, totaling roughly 360 billion dollars and growing. Research on warehouse functionality 40 years ago centered on palette loads and working with brick-and-mortar stores. Today, online shopping is a more personalized, customized experience and warehouse operations have had to innovate to meet the demand.
Optimizing pick-worker productivity
So if you’re a warehouse manager operating in this new e-retail environment, how can you make the most of your facility’s space and optimize pick-worker productivity?
In my study with co-author Santiago Gallino of Dartmouth College, we wanted to know more about the relationship between intra-bin search time and pick-worker productivity, an area that had not been explored previously. Many companies that use chaotic storage try to route their workers in some logical way, such as providing them with a list of items that are all in the same two aisles or sequencing the list so that the distance workers have to travel across the warehouse floor is minimized. For the pick-worker, searching through multiple items in congested bins can be challenging and time-consuming; we questioned if the degree of difficulty in the search had any effect on an employee’s productivity level.
Using data from an online women’s apparel company, we did a statistical analysis of warehouse and pick-worker activity over a nine-month period. Traditionally, managers attempt to minimize distance to improve worker productivity, but we discovered that that’s just part of the story: how long it takes employees to pick an item depends on how far the employees have to walk and how many items are in a bin once they get there. In other words, sending an employee to find a pair of jeans in a nearby bin with only 20 items makes sense. But if that bin contained 80 items, it might be better to route the worker to a farther bin with fewer items, simply because the employee loses more time rifling through a congested bin than he or she would by walking a greater distance.
Here are three main findings from our research that can help managers:
Searching matters. Chaotic storage carries an inherent search cost and time that can be predicted based on the number of items in the bin. This has not been accounted for in prior studies. Our research suggests that pick times increase by 16 percent as the search task difficulty level increases.
Walking further gives you a faster search. It seems counterintuitive, but sometimes a longer walk means a speedier pick time. Managers should focus on minimizing time, not distance.
Search time is highly dependent upon worker experience. The data shows that novices lose significant time going through packed bins, while the bin level, full or empty, mattered less for experts. The takeaway: search time matters for everyone but it really matters for novices.
And a final, big-picture consideration:
For managers, our study suggests there is significant value in retaining your workforce. If you can invest in areas that initially may cost you—salary, benefits, flex time—you will save money in the long term by maintaining a more experienced workforce. In an industry with a high degree of turnover, employee experience can be a huge asset.
Read the paper “Finding a Needle in a Haystack: The Effects of Searching and Learning on Pick-Worker Performance” published in Management Science.
Bob Batt is the Proctor & Gamble – Bascom Professor and an associate professor in the Department of Operations and Information Management at the Wisconsin School of Business.
Tags: