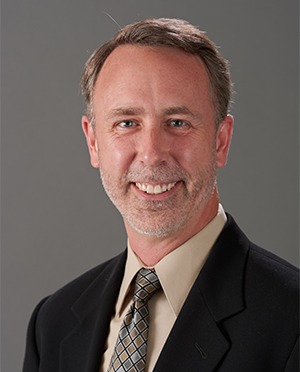
Over the past many months, the COVID-19 pandemic has wreaked havoc throughout the world. The human toll in terms of deaths and suffering has been tremendous, as has the strain put on our health care workers and first responders. The impact on the overall economy and businesses of all types has been tremendous as well, with some companies experiencing massive drops in revenue and many workers losing their jobs. I hope that you and your families have managed to stay healthy, and that the overall impacts on your companies, livelihoods and lives have been manageable.
Viewed through the lens of our professional community, it’s hard not to notice that the pandemic has brought supply chain management into the national conversation. As domestic shortages of N95 masks, face shields, gowns, and other types of personal protective equipment (PPE) began appearing as the virus started to spread, many people began thinking for the first time about the processes that make it possible for products to arrive where and when they are needed. Concerns about PPE shortages were quickly followed by ventilator shortages, as well as stories of limited supplies of COVID-19 tests (and then swabs for taking samples and chemicals for processing them). Then meat processing plants began to close due to virus outbreaks among workers, and concerns started to spread about the food supply. And throughout it all, everyone was on a quest to find that precious package or two of toilet paper on a store shelf.
This disease has led to the greatest disruptions to supply chains that I’ve seen in my lifetime. While companies have improved their supply chain risk management in the decade since some major events made headlines in 2011 – the earthquake and tsunami off the coast of Japan, and the flooding in Thailand that shut down about half of the world’s hard disk drive production – the impacts this time went much further. The virus affected many links in the supply chain at once (at the same tier and different tiers), and also hit both demand and supply simultaneously – often in different directions. Supply of masks was cut dramatically, while demand skyrocketed. Some parts of the food supply chain were pinched, while demand for commercial food evaporated and retail food demand spiked. Supply chains that were designed to be efficient under the assumptions of relatively steady demand and reliable supply struggled when these assumptions failed, and they often lacked the flexibility to shift existing supply into segments with surging demand.
The silver lining that I’ve seen in all of this has been the creativity that supply chain professionals have brought to address the problems, and the spirit of generosity and cooperation that has often accompanied that. Suppliers of PPE have worked hard to increase production and try to make sure items get to the places where they’re needed most. Individuals and groups of companies have reached out to offer their resources in any way that might help. Several of us here in the Center and others throughout UW-Madison have tried to offer our knowledge, insights and efforts to assist as well. Read about some of these efforts, along with some general reflections on disruptions to the PPE supply chain.
Now that we’ve experienced several months of this event, we also want to contribute to efforts that can help companies learn from what has happened, so that they can be better prepared next time. We’re exploring the development of new teaching materials (e.g., examples, case studies, simulations) related to supply chain risk and resiliency for use in future classes. In support of that effort, if you would be willing to share any stories you have about challenges your company encountered and how you addressed those, we’d be very interested in hearing from you.
In the meantime, I wish you health and a speedy recovery for your business and the broader economy.
Categories: