Supply chain managers don’t lose much sleep over normal day-to-day or month-to-month demand variations. Rather, it is the possibility of huge demand surges—caused by events such as severe weather, man-made disasters, new business partners, and viral products—that keeps supply chain managers up at night.
Random demand surges are important to understand because these surges can have a huge impact on operations and the bottom line. However, demand surges are rare, complex, difficult to predict, and nonrepeating. As a result, they cannot be perfectly predicted—no matter how thorough an organization’s planning. It is possible, however, to have a plan in place that positions organizations to best respond to those surges, whenever they do occur.
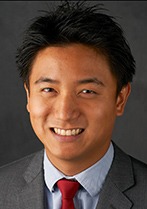
My research, published in Manufacturing & Service Operations Management, provides a framework for firms to prepare for a random surge. My colleagues Lu Huang of Google and Jing-Sheng Song of Duke University and I challenge the notion that these surges are indescribable random occurrences for which organizations are powerless to plan. We created a model that mathematically characterizes random surges and provides a strategy for preparedness.
We model surges two-dimensionally: magnitude over time. Traditionally, people think of a surge demand as just one number—how big is it? But with our research and modeling we also consider other factors: the duration of the surge, its intensity, its volatility, and its peak position, as well as one’s confidence in being able to predict each of these metrics.
Using these dimensions as metrics, we are able to demonstrate how an organization should design its supply chain in order to position itself to efficiently cope with random demand surges. We consider two fundamental strategies for preparing for demand surges: building reactive capacity and holding safety stock. Reactive capacity is the ability to ramp up production (above normal levels) when needed. On the other hand, safety stock is inventory that is held at all times and can be deployed when a surge occurs.
A firm can employ a combination of reactive capacity and safety stock. For example, a technology retailer we worked with not only holds extra machines in its own service centers (safety stock), but also compensates its vendors to hold additional components so that the vendors can quickly assemble the components into machines if needed (reactive capacity). Similarly, to prepare for disasters, humanitarian organizations both maintain safety stocks of key relief items at their own warehouses and contract with manufacturers for stand-by access to their production capacity should a disaster strike.
Our research helps organizations understand their own optimal planning strategy. If you input predictions on each metric, the model will output the optimal combination of reactive capacity and safety stock to employ. Thus, our research provides a general framework for managers and C-suite executives to think about the kinds of random surges their firms face and which strategies will be most appropriate to prepare for them.
It may seem counterintuitive to plan for something that is as random and unavoidable as demand surges. But if firms carefully consider the characteristics of surges that could occur, they can still prepare for them intelligently.
Read the paper “Supply Chain Planning for Random Demand Surges: Reactive Capacity and Safety Stock” published by Manufacturing & Service Operations Management.
Jordan Tong is an assistant professor in the Department of Operations and Information Management at the Wisconsin School of Business.
Tags: